In the ever-evolving landscape of engineering, conductive polyimide rods are establishing a significant niche for themselves. These high-performance components are gaining the attention of sectors that demand reliability and effectiveness, particularly in contexts where heat management and electric conduction are critical. As we shift from the prototyping phases of development into large-scale manufacturing, comprehending the advantages and functionalities of conductive polyimide resin rods becomes vital.
The aerospace industry, renowned for its high standards and challenging environments, can greatly benefit greatly from the use of these innovative materials. Conductive polyimide rods not only fulfill the stringent requirements for mass and durability but also perform exceptionally in their ability to resist extreme temperatures and oxidative conditions. As designers and engineers seek to improve their designs, the integration of these rods can lead to enhanced functionality and longevity in aerospace applications, ultimately contributing to more secure and optimized flight systems.
Features of Electrically Conductive Polyimide Rods
Electrically Conductive polyimide rods are renowned for their exceptional thermal stability, which makes them appropriate for demanding applications, especially in the aerospace industry. These rods can maintain their integrity and performance under harsh temperature fluctuations, ranging from -269 degrees Celsius to over 300 degrees Celsius. This property is essential for components that operate in hostile environments, ensuring dependability and longevity in aerospace applications.
Moreover, notable characteristic of conductive polyimide rods is their excellent electrical conductivity. Unlike https://telegra.ph/Why-Electrically-Conductive-Polyimide-Bars-are-Revolutionizing-Material-Science-06-06 , the addition of conductive fillers enhances their ability to conduct electricity while still retaining the merits of polyimide resin, such as structural strength and chemical resistance. This dual functionality makes them ideal for use in various electronic components, providing the necessary conductivity without compromising on mechanical integrity.
Additionally, these rods exhibit excellent mechanical properties, including high tensile strength and flexibility. This robustness allows them to tolerate various stressors encountered during manufacturing and in operational settings. The combination of top-performing attributes ensures that conductive polyimide rods can be shaped into complex shapes required in prototypes and final production parts, making them a preferred material in advanced technology development.
Uses in Aviation Industry
Conductive polyimide rods are gaining traction in the aerospace industry due to their distinct combination of lightweight properties and high thermal stability. These rods are vital components for various applications including insulation and electrical interconnections in aircraft platforms. Their ability to withstand extreme temperatures while maintaining functionality makes them appropriate for essential aerospace components that require reliable operation in demanding environments.
In addition to their physical applications, conductive polyimide rods serve a important role in the evolution of next-generation aircraft systems. The aviation sector stresses the need for materials that not only meet stringent safety standards but also contribute to energy efficiency. With their outstanding electrical insulation properties and lightweight characteristics, these high-efficiency polyimide rods are ideal for use in avionics and communication systems, enhancing overall system performance while reducing weight.
Furthermore, the inclusion of conductive polyimide rods in aerospace design allows for creative engineering solutions. Their adaptability enables designers to create more compact and efficient systems, such as unified sensor packages and multifunctional components. As the aerospace industry continues to move towards more green and advanced technologies, the reliance on materials like conductive polyimide rods will inevitably increase, clearing the way for the next generation of aircraft design.
Beginning with Pilot Designs to Manufacturing
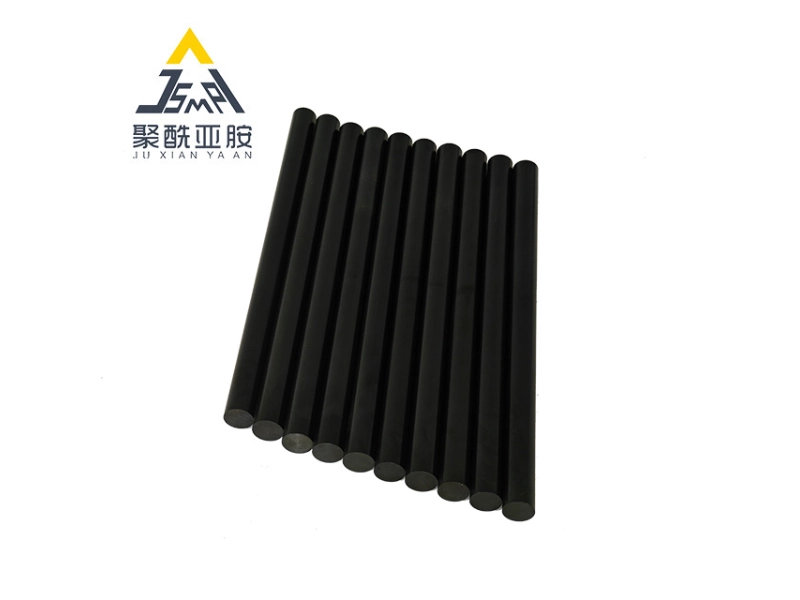
The transition away from initial models to production through the progression of conductive polyimide rods represents a crucial aspect that determines the substance's efficacy for real-world contexts. During the early prototype phase, engineers and designers examine the viability of employing superior polyimide rods, evaluating multiple compositions and configurations. This investigation enables adjustments in properties such as electric conductivity, adaptability, and heat resistance, making certain that the ultimate output satisfies defined demands for demanding contexts.
While production processes get refined, expanding production emerges as a crucial point of interest. The aerospace industry, especially, needs materials that can withstand severe conditions and maintaining operational integrity. Conductive polyimide rods are employed in this sector due to their light nature and excellent mechanical properties. https://bang-bitsch.mdwrite.net/conductive-polyimides-bars-discovering-new-opportunities-in-engineering to create these rods in large quantities while maintaining standards of quality becomes crucial, as even little inconsistencies in material functionality may lead to major issues in aerospace applications.
Once the production process becomes optimized, the emphasis shifts to quality control and compliance with regulatory standards. Conductive polyimide rods must go through thorough testing to guarantee they fulfill the strict regulations set forth by aerospace authorities. This entails heat cycling, mechanical stress testing, and tests for electrical conductivity. Valid validation paves the path for large-scale production, enabling the broader use of these innovative materials, which not only enhance performance while also enhance the general reliability of aerospace systems.
Future Developments in Polyimide
As the demand for light materials grows, the prospects of this technology seems bright. Innovations in the creation of electrically conductive polyimide rods are expected to enhance their uses across various sectors, particularly in the aerospace industry. With ongoing investigations focused on improving heat resistance and physical characteristics, next-generation polyimide rods may become even more capable in harsh environments, paving the way for their utilization in high-tech aerospace systems.
The combination of smart materials and coatings into polyimide technology will also play a vital role in the progress of these rods. By incorporating sensors or self-healing features, conductive polyimide rods can become capable of multiple functions, offering not only strength but also advanced surveillance and maintenance capabilities. This movement will be particularly beneficial in the aerospace industry, where safety and reliability are of utmost priority.
In addition, the trend toward eco-friendliness in production will affect the production of polyimide materials. Researchers are examining bio-based raw materials and eco-friendly processing techniques, aiming to reduce the ecological footprint of polyimide synthesis. As the industry shifts towards greener methods, the introduction of sustainable conductive polyimide rods could lead to wider adoption and application in multiple sectors, ensuring that these materials remain at the cutting edge of progress.